윤활유 용기에 꿈과 포부를 담다!! – GS칼텍스 윤활유 공장 김구희 사원
내용물만큼이나 그것을 담아내는 그릇은 중요한 역할을 합니다. 국내 시장점유율 1위의 자리를 당당히 지키며 글로벌 Top 5를 향해 전세계로 뻗어나가고 있는 GS칼텍스 윤활유. GS칼텍스 윤활유 공장의 김구희 사원이 빚어낸 용기에 담긴 윤활유는 새로운 생명력을 얻습니다. GS칼텍스의 자랑스러운 도예공, 김구희 사원을 지금 만나러 갑니다. C-:
“2011년 12월에 입사해서 윤할유 생산계획을 9개월 정도 하다가 윤활유 용기 생산계획, 원부자재 구매 및 재고관리 업무를 맡게 됐어요. 기존에 용기 관련 업무를 일괄 처리하던 자회사의 업무를 우리 회사가 처음으로 직접 처리하게 된거죠.”
김구희 사원은 용기 업무를 총괄하는 정기훈 계장과 설비 관리와 정비를 담당하는 이병훈 사원과 함께 단촐한 팀이 꾸려졌다고 이야기합니다. 영업부서에서 윤활유 판매계획을 수립하면 그에 맞게 윤활유 생산계획을 짜고, 윤활유를 담아내는 용기는 생산에 앞서 3일 이전에 준비가 되어 있어야 합니다.
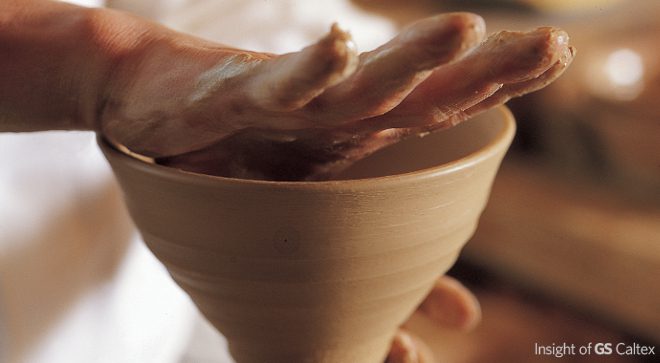
“총 100여 가지의 용기를 생산하고 있는데요. 색상, 금형, 라벨, 규격도 제각각이고 설비마다 나올 수 있는 용기도
달라집니다. 이러한 틀 안에서 불필요한 작업을 최소화시키면서 용기 생산량은 최대한으로 끌어올리는 효율적인 생산계획을 짜는 것이 목표에요.”
진정 효율적인 생산계획이 되기 위해서는 현장 직원들의 의견이라는 양념이 꼭 더해져야 한다고 말합니다.
“제가 알고 있는 범위 내에서 효율적으로 계획을 짠 뒤에 그걸 가지고 꼭 현장으로 갑니다. 예를 들어 이렇게 생산을 하면 주말 동안에 수작업이 많이 발생하게 된다는 이야기를 듣게 되죠. 제가 미처 고려를 못 했던 부분들에 대한 의견을 들을 수 있기 때문에 합당하다고 생각되는 부분이 있으면 즉각 반영을 하고 수정을 합니다.”
용기 업무를 맡은지 1년이 되어 가는 김구희 사원. 하지만 처음 계획대로 동일하게 이행된 적이 거의 없다고 말합니다.
“여러가지 변수가 많고 순간순간 문제가 생기면 계획이 틀어져 버리니까 수시로 모니터링을 해야해요. 가령 설비가 고장나면 긴급하게 계획을 바꿔야 합니다. 가만히 손 놓고 있다간 용기 공급이 안 돼서 윤활유 충전이 안 되는 대형사고가 터지는 거죠. 이런 상황을 신속하게 파악하고 적절하게 대응하는 능력이 정말 중요합니다.”
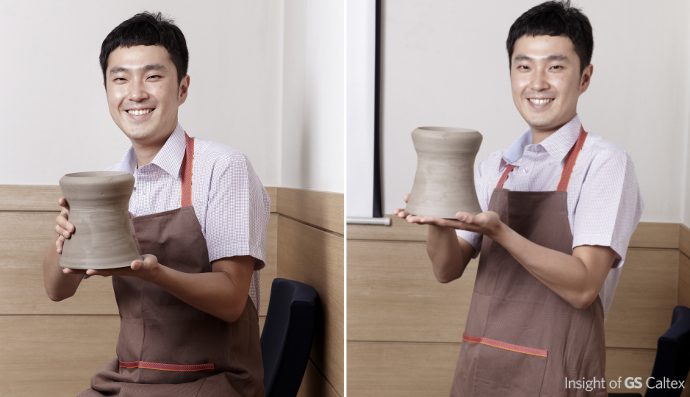
“공장은 24시간 풀가동 되니까 전날 야간에 발생한 일은 알 수가 없어요. 아침에 출근하면 현장에 제일 먼저 들려서 오늘 아침에 만들기로 했던 계획대로 수량과 품질이 제대로 나오고 있는지를 확인하는 작업부터 합니다.”
효율적인 생산계획만큼이나 중요한 업무가 원부자재 구매와 재고관리 업무라고 말합니다. “이렇게 용기 생산계획이 수립되면 총 200여 가지에 이르는 원부자재를 미리 구매해서 준비를 해둬야 합니다. 넘치지도 모자라지도 않게 적정재고를 유지하면서 미리미리 발주하고 월말에는 재고실사를 수행합니다.
회사의 원부자재가 제 돈이라는 마음가짐으로 관리하고 있어요. 매월 발생하는 원부자재 로스의 원인을 찾아내고 최소화해야 하죠. 그러기 위해서는 용기별로 투입되는 원부자재의 중량과 수량 숙지는 기본입니다.”
쉬운 이해를 위해 설명 들어갑니다! 예를 들어 100그램 중량의 용기를 만들 때 HDPE이라는 수지가 97%, 나머지 3%는 색상을 내는 재료를 투입합니다. 계산대로라면 색상을 내는 재료가 월말에 어느 정도 남아있어야 하는데 막상 재고실사를 해보면 부족한 경우가 발생합니다. 재료 중량은 미량이더라도 생산하는 용기 전체 수량이 워낙에 많다보니 재고 차이가 발생할 수 있다는 겁니다. 이렇게 재고 차이를 잡아내고 원인을 파악해서 반복되지 않도록 방지하는 것도 그의 역할입니다.
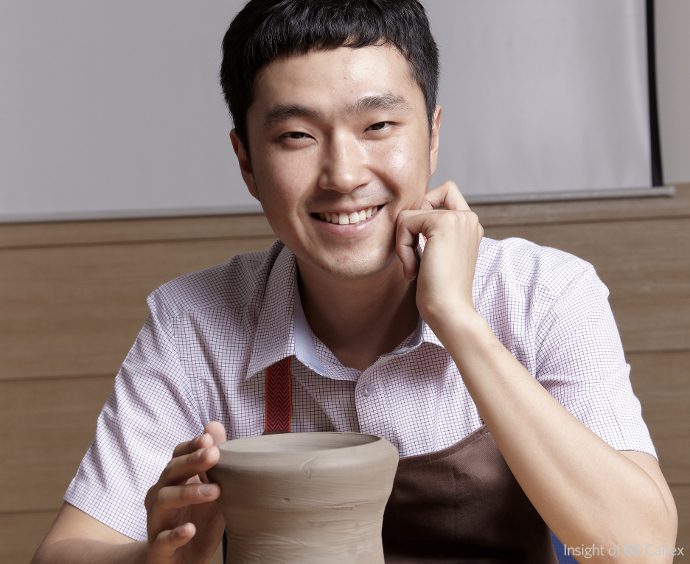
“구멍이 가장 대표적인 불량이에요. 그 중에서도 가장 두려운 것이 미세구멍인데요. 처음에 윤활유를 충진할 땐 새지 않다가 박스에 담고 팔레트에 적재해서 하중을 가하면 얇은 접착부위가 터지면서 윤활유가 샐 수 있어요. 불량 원인을 파악하고 꼼꼼하게 조치하고 검사해서 불량을 최소한으로 줄여 나가고 있습니다.”
원체 꼼꼼하고 차분한 김구희 사원이지만, 자잘하게 챙기고 처리할 사항이 많은 용기 업무를 하면서 더욱 깐깐한 성격으로 변했다며 웃습니다.
“용기를 12,000개를 만들어야 하는데 실수로 1,200개로 적었다면 곧바로 대형사고가 터지죠. 숫자 하나에도 조심조심해야 합니다. 또 용기는 저희 세 사람만 담당하고 있으니, 용기 관련 문의와 요청이 많이 들어옵니다. 하나하나 놓치면 안 되니까 포스트잇에 메모했다가 하나씩 처리하고 떼어버리죠. 한 건이라도 놓치면 여러 사람이 고생하게 되니까요.”
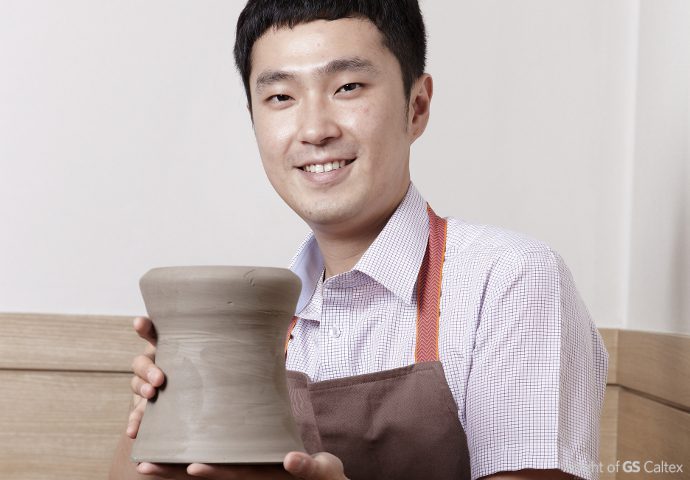
“윤활유 용기는 공장에서도 난생 처음 다루는 품목이었어요. 정말 아무것도 모르고 업무를 받았는데 기초적인 지식도 없고, 주변에 여쭤볼 선배도 없었어요. 윤할유 생산계획은 프로세스가 전부 정립돼 있으니까 하나하나 배워서 숙지하고 실행해보고 그랬죠. 그런데 용기 쪽은 말 그대로 맨땅에 헤딩을 해야 하는 상황이었어요. 처음 3개월은 밤잠을 설칠 정도로 정말 힘들었습니다.”
막막하고 엄두가 안 나는 상황에서 책, 인터넷, 현장 직원까지 수단과 방법을 가리지 않고 공부하고 수소문하고 벤치마킹하기에 이릅니다.
“SAP 자재번호부터 시작해서 계획문서, 발주문서, 재고관리문서 생성까지 아예 프로세스를 만들어내기 시작했죠. 기억해보면 고생도 정말 많이 하고 시행착오도 많이 겪었지만 덕분에 저희 손으로 만들어냈다는 자부심도 강하죠.”
이제는 어느정도 업무의 틀이 잡혀 새로운 업무에도 욕심을 내고 있다고 말합니다. “4리터 용기 디자인이 단순한 사각형이었어요. 디자인 변경을 위해 기존 설비를 철거하고 신규 설비를 들여왔어요. 정비 업무를 맡고 있는 병훈이도 고생을 많이 했고, 처음에는 계획대로 생산이 잘 안 나와서 고생을 좀 했습니다.
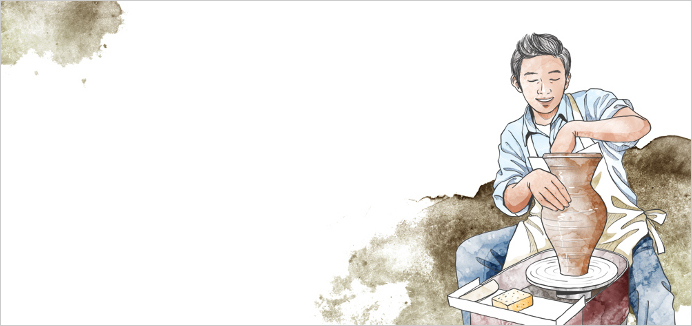
3개월 노력 끝에 신규 디자인 용기가 처음으로 문제없이 나왔을 때 어찌나 뿌듯했는지 몰라요. 디자인이 훨씬 더 고급스럽고, 크기도 더 커보이구요. 주입구도 커지면서 넘치는 현상도 방지해주고 있어요. 앞으로도 다른 용기들도 개선 포인트를 계속 찾아나가서 최적화시켜야죠.”
용기의 시작부터 철저하게 경험하고 프로세스를 만들어낸 김구희 사원. 그래서인지 관심과 애정이 남다릅니다.
“시중에 판매되고 있는 저희 윤활유를 보면 내가 만든거라며 가족과 친구들에게 은근히 자랑을 해요. 하하. 장보러 마트에 가서도 플라스틱 용기만 보게 되고요. 세제랑 화장품 용기를 이렇게 만들었네? 이런 아이디어는 윤활유 용기에도 적용할 수 있지 않을까? 이런 생각도 하죠.”
김구희 사원이 그가 가진 당찬 꿈을 이야기합니다. “공장 분들의 땀과 노력이 들어간 제품이 우리나라뿐만 아니라 전세계를 누비는데 작은 부분이지만 기여하고 있다는 생각에 보람을 느끼죠. 용기뿐만 아니라 윤활유 전반에 대해 경험하고 배우면서 글로벌 Top 5를 목표로 열심히 해보고 싶습니다.”
GS칼텍스 윤활유 용기를 책임지고 있는 그의 용기와 도전정신를 응원합니다! C-: