그리스 제품 균질화 장치 설치를 통해 품질과 생산성 향상을 이뤄내다 – GS칼텍스 그리스 공장
장인정신, 현대적 언어로 재해석하면 자신이 하는 일에 최선을 다해 최상의 상품을 만들어내는 전문가적 직업정신이라 할 수 있습니다. 하지만 생산자의 장인정신 못지 않은 사용자의 장인정신이 현장에서 빛을 발한다면? 외부에서 구매·설계·시공한 자재나 설비를 공장에 최적화시키는 과정에 투입된 GS칼텍스의 장인정신을 돌아봅니다. 자체 개발한 균질화 장치를 그리스가 이송되는 과정에 설치함에 따라 품질과 생산성 향상이라는 두 마리 토끼를 잡은 그리스 공장에서 GSC표 장인정신을 만나봅니다.
반응ㆍ냉각ㆍ혼화ㆍ균질ㆍ충전, 그리스 제조의 핵심
인천 북성동에 위치한 그리스 공장. 1986년 4월 일본 쇼와쉘과의 기술제휴로 연간 3천 톤 규모의 생산설비로 준공되어 자체 품목 개발과 설비 합리화를 통해 2013년 현재 4개 품목 30여 제품을 연간 7천 톤 가량 생산해내고 있습니다. 30여 년 사이 큰 투자재원 없이 생산규모를 두 배 이상으로 늘렸고, 기술 개발을 통해 자체 브랜드 제품을 내수와 수출용으로 활발하게 생산하고 있는 것입니다.
그리스 제조공정은 반응기, 냉각기, 혼화기, 균질기, 충전기의 다섯 가지로 나뉩니다. 기유를 지방산과 금속수산화물과 고온에서 반응시켜 반고체의 금속비누를 형성하는 반응기, 이를 온도조절을 통해 정해진 속도로 냉각하고 교반을 통해 원하는 금속비누 섬유구조를 형성하는 냉각기, 기포와 이물질을 제거하고 성능을 향상시키는 첨가제를 투입하는 혼화기, 물리적인 힘인 전단력을 가해 금속비누 섬유길이를 일정하게 맞춰주고 고르게 분산시키는 균질기, 마지막으로 제품을 용기에 포장하는 충전기의 과정을 거칩니다.
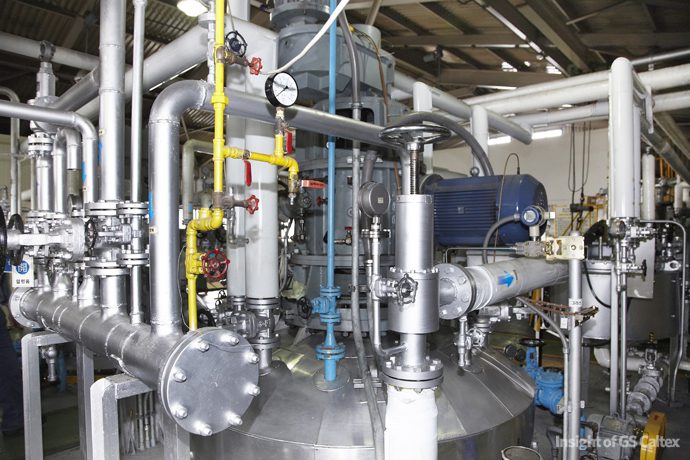
토요일 생산 1 batch를 더 늘려라
그리스 공장의 생산능력은 하루 3 batch로 한달 25일 조업기준으로 볼 때 월 2,500드럼을 생산해냅니다. 하지만 지난해 판매량이 월 2,500드럼을 육박했고 이번해 판매예측량은 34%가 늘어난 월 3,100드럼에 이르렀습니다. 생산량이 늘어남에 따라 그리스 공장 작업자들은 휴일 없이 일을 해야 하는 상황에 쳐했고, 안전사고의 위험도 함께 높아졌습니다.
그리스 생산규모 확대가 절실한 상황에서 최소비용으로 설비를 개선해서 생산량을 증대하는 방안을 연구하게 됩니다. 그러던 중 토요일 2 batch 생산을 3 batch로 늘릴 수 없을까라는 고민이 시작됩니다.
토요일 야간 batch 생산은 공장을 가동하지 않는 일요일 하루 동안 꼬박 제품을 혼화기에 보관해야 하므로 적정 품질 확보가 어려웠습니다. 그래서 2 batch만 생산한 뒤 반응기 가동을 중단하여 월요일 오전에 재가동을 하고 있었습니다. 균질화 과정을 거치지 않은 상태로 제품을 방치하면 품질 확보가 되지 않는 문제 때문이었습니다. 즉 균질화 과정 없이는 그리스 외관이 거칠어지고, 전단안정성 규격을 충족시키지 못하기에 제품화를 위해 가장 중요한 공정입니다.
균질기를 자체 개발하다
냉각기와 혼화기 사이 배관에 간이 균질기를 설치해서 그리스를 이송하는 과정에서 자연스럽게 전단력을 받도록 하면 어떨까하는 아이디어가 스쳐 지나갔습니다. 즉 겔화된 그리스를 미세한 필터를 통과하게 하여 전단력을 가함으로써 제품의 균질성을 향상시켜 품질안정성을 높이는 균질기의 원리에 착안, 균질기의 노즐구조와 유사한 형태로 1/3 크기로 축소된 밸브를 제작하고 설치하여 테스트를 실시하기에 이릅니다.
이 과정에서 전문서적을 파헤치고, 균질기를 완전 분해해서 구조를 파악하고 모형을 만들어내고, 국내 균질기 제작업체로부터 기술 자문을 확보하고, 균질기의 원리를 교육받으며 밸브 설계에 필요한 전문지식을 전수받습니다.
생각과 실제가 매치가 안 되는 경우가 부지기수로 발생하고, 그런 과정에서 시행착오를 겪고, 반복적으로 수정하고 변경하며 안정화 단계에 접어들었습니다. 가령 전단력이 밸브의 구경과 각도 등에 굉장히 예민하게 반응했고, 장력이 너무 세면 그리스가 이송되지 않고, 장력이 너무 약하면 전단력이 떨어지는 문제가 발생했습니다.
생각지도 못한 수많은 변수들을 하나하나 테스트하고, 샘플을 채취하고, 물성치를 점검하는 과정으로 이어졌습니다. 수시로 설비를 풀고 조립하는 과정을 반복하며 현장에서 비지땀을 흘리며 고생한 기억도 생생합니다.
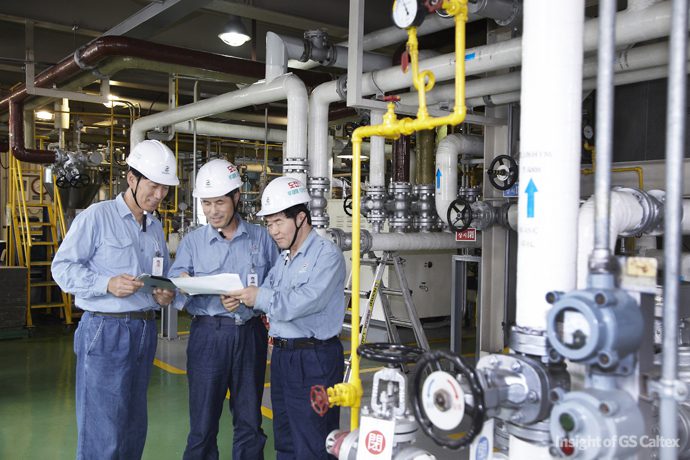
그리스 공장 직원들이 주축이 되어 아이디어를 짜면 제작업체에서 가공을 하고 테스트와 시운전까지 반년이 넘는 기간이 소요됐습니다. 마침내 이번해 6월 실제로 밸브가 작동을 하면서 토요일 생산을 2 batch에서 3 batch로 늘림에 따라 월 150드럼이라는 생산량 증가와 균질화를 통한 품질개선이라는 결실을 맺었습니다.
최근에는 동일한 균질기를 혼화기와 균질기 사이 배관에도 설치해서 균질작업을 보완하기에 이르렀습니다. 현장에서 생각해낸 아이디어에 그치지 않고, 실질적인 설비 개선으로 이어져 눈에 보이는 성과를 일구어냈다는 깊은 긍지와 자부심까지 덤으로 얻었습니다.
GS칼텍스 그리스의 빛나는 미래를 위하여
그리스는 ‘손가락 끝의 예술(Art of thumb)’이라고 불릴 정도로 경험과 육감에 의해 많은 부분이 좌우됩니다.
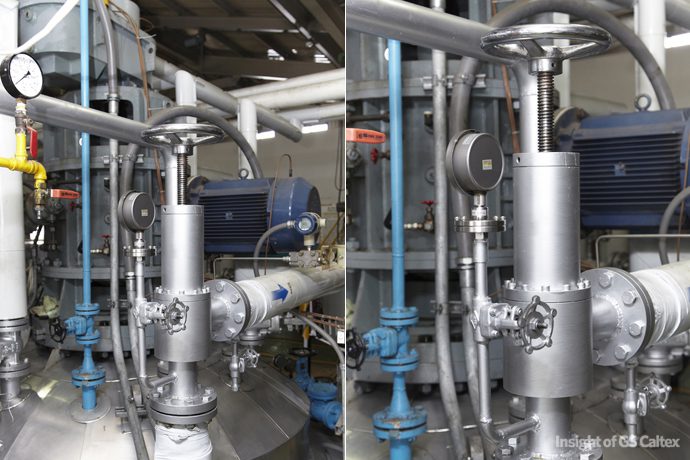
실제로 그리스의 주도를 측정할 때 검지와 엄지로 시료를 만져보고 그 감각으로 미묘한 제품간의 차이를 구별해냅니다. 이렇게 공정 하나하나의 과정을 육안으로 보고, 소리를 듣고, 손으로 만져보고, 냄새를 맡아가며 품질을 맞춰냅니다. 같은 사람이 같은 방법으로 만들어도 똑같은 제품이 나오지 않는 그리스는 표준지침서나 절차서가 있지만 표준화되기 힘든 항목 중에 하나입니다.
원료들의 물성치도 제각기 다르고, 반응하는 과정에서 온도, 압력, 시간에 따라 오프스펙이 나오기 쉽다. 다양한 현장 경험을 토대로 생산 관리, 원부자재 관리, 제품 입출하, 예방정비, 제품 개발과 시험까지 다양한 업무를 소화해내는 스킬을 가지고 있는 그리스 공장 구성원들. 총 10명의 전문가들이 이끌어가고 있는 그리스 공장은 1년에 1,000 batch를 생산하지만 오프스펙으로 인한 재배합이 지난 몇 년간 0건일 정도로 무결점 생산을 자부합니다.
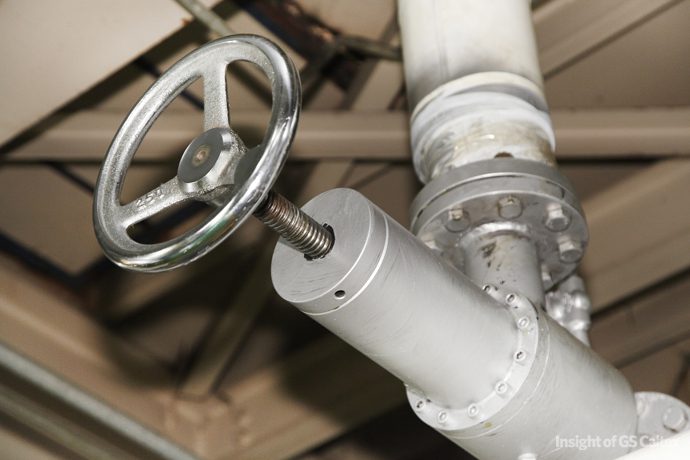
그리스의 A부터 Z까지 철저하게 파고들고 연구하고 개발하는 구성원들의 장인정신이 그리스 공장의 가장 소중한 자산입니다. 앞으로도 창의적인 업무 혁신 활동을 통해 고부가가치 제품을 개발하고, 설비를 합리화하고 확장해서 최고의 제품을 최대한 생산해서 회사 발전에 기여하겠다는 다짐이 큰 보람이자 동기부여가 된다고 말하는 구성원들. 그들의 노고와 땀방울에 존경과 감사의 마음을 보냅니다.